After years of turbulent supply chains and a rush to invest in electric vehicle manufacturing, automakers are scaling back production plans in the face of slowing EV demand.
They’re also continuing their push to move supply chains away from China in a bid to comply with stricter Inflation Reduction Act tax credit requirements.
Read on for the top manufacturing and supply chain trends set to shape the auto industry in 2024.
U.S. automakers are scaling back their EV plans
General Motors, Ford and others are putting the brakes on some of their EV production plans as consumer adoption lags behind expectations.
Ford, for example, announced in September it was pausing construction of its $3.5 billion EV factory in Marshall, Michigan, after sluggish sales of its F-150 Lightning and other EVs prompted it to roll back its $50 billion production expansion plans.
“Ford electrified their F150 because it was one of the best selling pickup trucks in the country, maybe in the world,” Adam Ragozzino, Principal Analyst, Batteries & e-Powertrains, Wards Intelligence, said in an interview. “But an electric pickup isn't really what mainstream pickup truck owners wanted. You know the guys that are working out of their truck towing, hauling tools, whatever it is, that doesn't fit the bill for them.”
GM has made similar moves, announcing in October that it was abandoning plans to produce up to 400,000 EVs through mid-2024 as the company tries to balance market demand and profitability.
Compounding the rival automakers' problems is the growing number of competitors vying for U.S. EV market share.
“The legacy OEMs really need to take an ordinate amount of market share to maintain their current market share,” Ragozzino said. “ My prediction is if they don't get a mainstream [EV] on the market soon, they're going to find themselves with a lot less market share overall than they've ever had.”
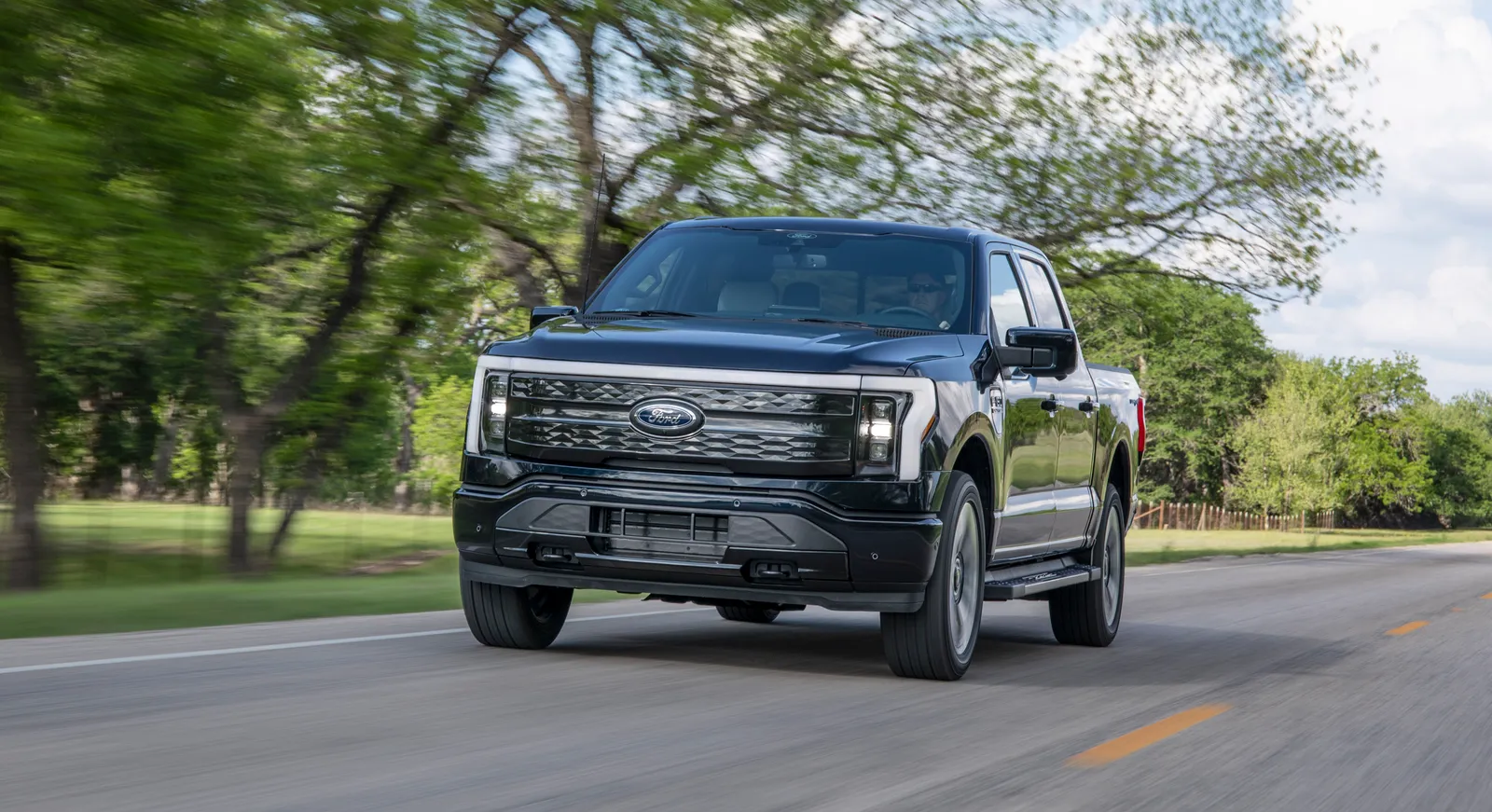
Automakers will continue with nearshoring and reshoring efforts
Automakers and suppliers are likely to continue to reshore and nearshore their operations, especially in Mexico, to reduce their financial risks by shortening their supply chains, said Dan Hearsch, partner and managing director at consulting firm AlixPartners.
Such strategies often lower freight costs, which have increased in recent years as freight prices have become more volatile, Hearsch said.
They can also help companies abide by made-in-America and related provisions in federal policies and programs, such as the CHIPS and Science Act and Inflation Reduction Act.
Yet it can be challenging to establish supply bases in Mexico, as many of the largest suppliers already have as much business as they can support, Hearsch said.
“It feels a little bit like China in the ’80s and ’90s, where if you weren't there relatively early you had to go invest time to develop relationships just to get companies to answer your RFP,” Hearsch said. “We're seeing companies go from just trying to source in Mexico to setting up their own operations.”
Adding to these challenges is the competitive labor market.
“You've got to deal with the fact that there's only so much labor, and there's so much demand for companies trying to get a piece of that manufacturing pie,” Hearsch said.
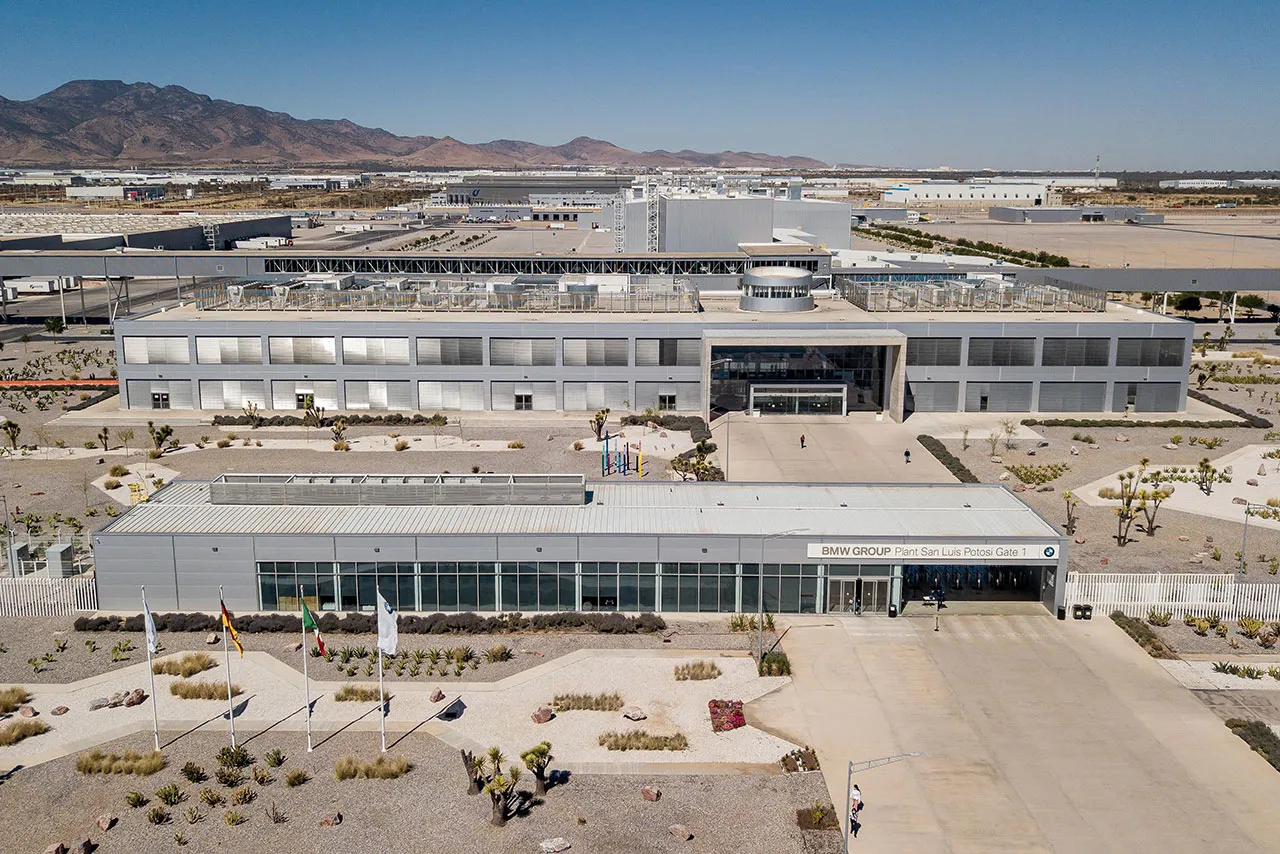
EV battery recycling will grow as automakers try to cut costs and meet sustainability goals
As more automakers look to decrease their reliance on China-based suppliers for raw materials such as cobalt, nickel and graphite, automakers are looking for new ways to fulfill their critical mineral needs for battery production. One solution is battery recycling initiatives in the U.S.
In August, battery recycler Redwood Materials announced it raised over $1 billion in a Series D funding round. The funds will be used to expand the company’s U.S. battery supply chain, allowing customers to buy recycled battery materials domestically for the first time.
Redwood Materials says its technology can recover roughly 95% of nickel, cobalt, lithium and copper from end-of-life EV batteries, which can reduce the costs of producing new ones.
“I think it's going to be a massive industry,” said Steve Patton, Americas Mobility Sector Leader at EY. “And if you think about the cost and the scarcity of the minerals that we need to get, we have to go do this.”
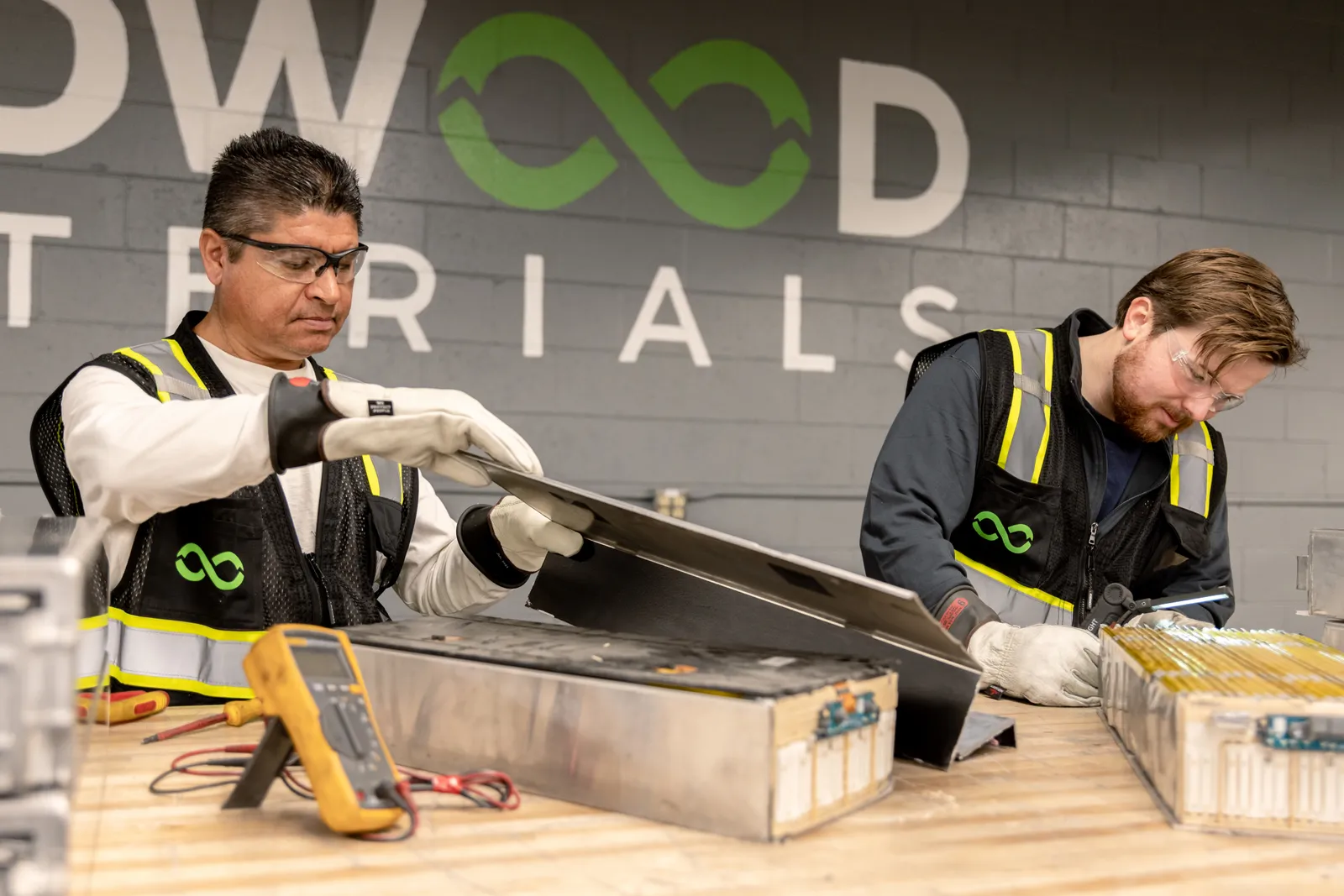
Redwood aims to produce 100 GWh of cathode and anode components per year by 2025, which is enough to manufacture battery cells for around 1 million EVs annually. The company is targeting 500 GWh a year by 2030, which is enough for five million EVs.
Patton noted that automakers may want to retain the rights to these critical raw materials once they are sourced for battery production or even at the time of mining.
“They're trying to create almost closed cycle loops around who owns the minerals once they enter their ecosystem,” Patton said. “And so that is going to be an interesting challenge, too, who has the rights to these recycled minerals.”
Disclosure: Informa is the owner of Automotive Dive's publisher, Industry Dive, and Wards Intelligence. Informa has no influence over Automotive Dive's coverage.